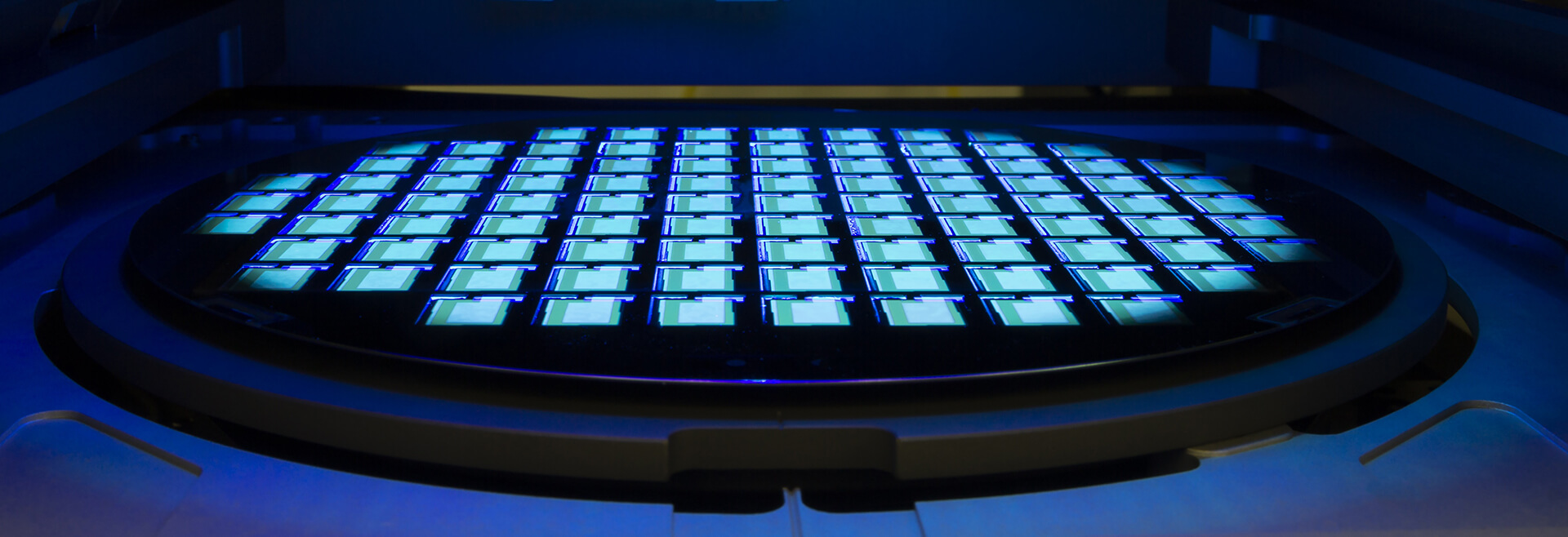
Coater Systems—Ultra C ct

For wafer level packaging applications
Advanced double-coat spin-coating technology
ACM’s semiconductor coating systems perform crucial steps in the lithography process during wafer level packaging (WLP). These easy-to-use tools provide an even coating of photoresist chemistry using innovative double-coat spin-coating technology.
The ACM coating tool enables the following processes:
- HMDS application
- Photoresist coating /polyimide coating
- Soft bake
The coating process is the first and most crucial step in WLP, and it determines the quality of all the processes that follow, which is why ACM incorporates a number of special features and modules for optimizing the coating step. For example, the coating systems provide edge barrier removal (EBR) with absolute precision, and the tool’s core technologies allow it to help customers increase throughput while decreasing cost and downtime.
Major Benefits
Innovative coating method
ACM uses an innovative spin coating method, which coats the wafer twice. This improves the uniformity of HMDS and photoresist coating to eliminate bulge, depression, or “W” errors.
Precise coating control
This tool is designed to help easily control the thickness and uniformity of the coating, providing a better quality product. It contains state-of-the-art chemical temperature and flow rate control systems to ensure chemicals are released in the desired amount and at the desired temperature throughout the process.
Auto-clean capability
This proprietary feature automatically cleans the single-wafer chamber, removing all excess HMDS and photoresist that has been spun off during the process. The benefits of using our auto-clean system compared to manual cleaning are:
- Significantly increased throughput
- Increased uptime, reduced time and cost for chamber cleaning
- Eliminates human errors from disassembly/reassembly
- Increased employee safety
Hot/Cold Plate module
An important part of the tool, the Hot/Cold Plate module is controlled by a stepper motor that precisely controls the wafer’s spin speed and position. The module provides precise temperature control and uniform exhaust control to ensure a quality soft bake process.
Superior technology
This system incorporates advanced component modules such as high-precision wafer transfer systems, superior fan filter & exhaust units, and independent control of process environment for each chamber. All these modules are designed for ease of use while delivering the desired coating thickness and uniformity. Easily customizable software also allows the tool to easily integrate into the production line.
Protecting the environment, reducing costs
ACM is committed to helping protect our world’s environment. Hence, all our machines are fitted with chemical recycle and filter systems that reuse chemicals and decrease waste—and also decrease the user’s costs. ACM’s fan filter and exhaust unit removes evaporated chemicals and replaces them with contaminate-free filtered air.
Features & Specifications
- 8” and 12” wafer compatibility
- Process module includes:
- 1 to 4 sets of coating chambers including:
- Auto-cleaning function
- ULPA FFU in each coating chamber
- 1 to 2 types of PR nozzles in each coating chamber
- EBR and BSR nozzles
- Pre-wet nozzles
- Front-side and back-side cleaning nozzles
- 8 to 14 hot plates
- 2 to 4 cold plates
- 1 to 2 HMDS modules
- 1 to 4 sets of coating chambers including:
- Chemical and plumbing module including:
- 2 to 6 sets of PR pumps with de-bubbling systems
- 2 to 6 sets of chemical delivery units for EBR, pre-wet or chamber auto-cleaning
- Wafer transfer module including:
- 1 to 4 load ports
- Optical wafer-centering aligner
- Robot with 2 to 4 vacuum or mechanical arms
- ULPA FFU in robot bay
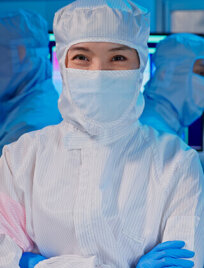
Contact Us
Looking for customized solutions for your wet wafer processing, ECP, Furnace, Track and SFP?