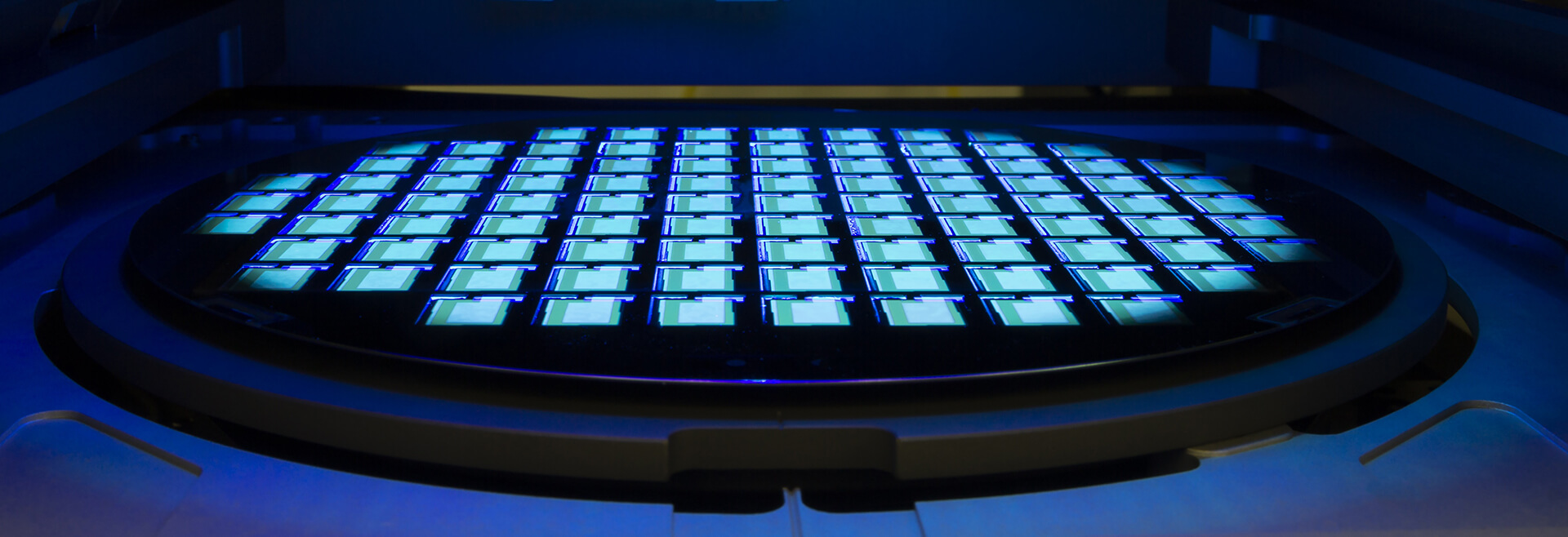
Stress Free Polishing Systems—Ultra SFP

For advanced packaging applications
Stress-free polishing and CMP in a single system
Built on our proven stress-free polishing (SFP) technology, the Ultra SFP is designed to address common yield issues associated with through-silicon via (TSV) processes and fan-out wafer-level packaging (FOWLP). These include copper overburden post-TSV fill and wafer warpage issues with FOWLP processes.
ACM’s Ultra SFP can be integrated with an external chemical mechanical planarization (CMP) system and ACM’s wet-etch system into one single system. Its proprietary electrochemical mechanism delivers electrolytes and a power source to the wafer simultaneously, as it rotates on the chuck, to electrically remove metal ions from the wafer surface.
Ultra SFP provides a safer CMP alternative
Conventional CMP creates challenges for chemical usage and disposal. Toxicity levels and decomposition issues of CMP process chemistries make their disposal difficult.
The Ultra SFP’s built-in recycling system solves these issues. Electrolyte and wet-etchant chemistries are recycled through the system and reused in real time, to significantly reduce the overall usage of chemicals and consumables.
Ultra SFP applications
The Ultra SFP provides an environmentally friendly alternative to conventional CMP for TSV and FOWLP.
In TSV applications, SFP is used to remove bulk copper overburden (post-TSV fill) down to 0.2µm. Next, CMP is used to planarize the wafer and remove the remaining copper down to the titanium barrier layer. Finally, a wet-etch step is performed to remove the titanium and expose the oxide layer.
In FOWLP, this same sequence of process steps can be used to eliminate wafer warpage, remove copper overburden and planarize redistribution layers.
Major benefits
Less process stress
ACM developed the unique three-step approach used by the Ultra SFP to effectively eliminate any process-induced stress to the wafer.
Environmentally-friendly
With its built-in electrolyte recycle and reuse system, the Ultra SFP consumes significantly fewer chemicals during processing. This makes the tool a much more sustainable and environmentally-friendly option for CMP and wet etch.
Lower cost of ownership
Because it processes chemicals so effectively, the Ultra SFP greatly reduces chemical usage and waste, as well as enhances consumable recycling. The system’s ability to reclaim removed metals, which can then be used for other purposes, heightens its sustainable nature.
Features & Specifications
- Comprises two SFP chambers, one CMP station and two wet-etch/clean chambers
- Utilizes a range of process chemistries:
- Electrolytes
- Copper slurry
- Copper etchant
- Titanium etchant
- Removal rate = 0.5µm/minute
- Within-wafer nonuniformity < 3%
- Wafer-to-wafer nonuniformity < 1.5%
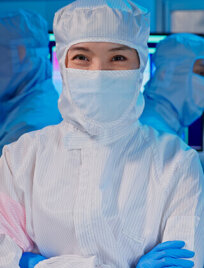
Contact Us
Looking for customized solutions for your wet wafer processing, ECP, Furnace, Track and SFP?